Leading Smls Pipe and fittings supplier from China since 1991
Understanding Oil Well Tubing: A Comprehensive Guide to Tubing Types, Applications, and Maintenance
Understanding Oil Well Tubing: A Comprehensive Guide Oil well tubing is crucial in the oil and gas industry, as it plays a pivotal role in the extraction of hydrocarbons from underground reservoirs. This guide aims to provide a thorough understanding of oil well tubing, delving into its types, applications, maintenance practices, and factors to consider in its selection. Table of Contents What i
Jul 05,2025
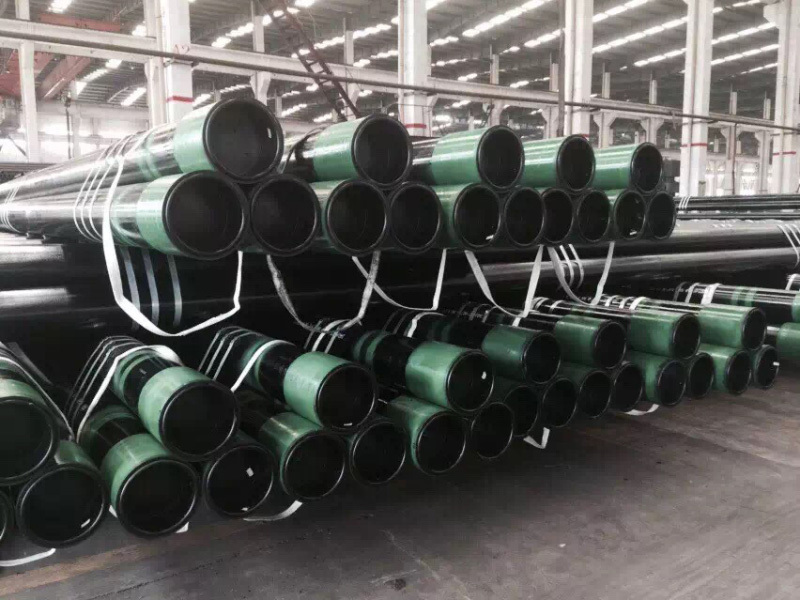
Understanding Oil Well Tubing: A Comprehensive Guide
Oil well tubing is crucial in the oil and gas industry, as it plays a pivotal role in the extraction of hydrocarbons from underground reservoirs. This guide aims to provide a thorough understanding of oil well tubing, delving into its types, applications, maintenance practices, and factors to consider in its selection.
Table of Contents
- What is Oil Well Tubing?
- Types of Oil Well Tubing
- Applications of Oil Well Tubing
- Key Features and Specifications
- Maintenance Practices for Oil Well Tubing
- Best Practices for Selecting Oil Well Tubing
- Common Challenges and Solutions
- Future Trends in Oil Well Tubing
- Frequently Asked Questions (FAQs)
- Conclusion
What is Oil Well Tubing?
Oil well tubing refers to the piping systems used in oil wells to transport crude oil and gas from the reservoir to the surface. It provides support for the wellbore, protects against external pressures, and ensures the safe and efficient flow of hydrocarbons. The tubing is installed within the casing, which is the outer layer of the well, and is designed to handle high pressures and corrosive substances.
Types of Oil Well Tubing
Understanding the various types of oil well tubing is essential for selecting the right one for your needs. Each type has its unique properties, applications, and associated costs.
Carbon Steel Tubing
Carbon steel tubing is one of the most widely used types of tubing in the oil industry due to its strength and durability. It is relatively inexpensive and can withstand high pressures, making it suitable for most environments. However, carbon steel is prone to corrosion, particularly in acidic or saline environments.
Stainless Steel Tubing
Stainless steel tubing is known for its excellent corrosion resistance and durability. It is often used in harsh environments where carbon steel may fail. While stainless steel is more expensive than carbon steel, its longevity and resistance to corrosion make it a preferred choice for many operators, particularly in offshore drilling applications.
Fiberglass Tubing
Fiberglass tubing offers a lightweight alternative to traditional metal tubing. It is highly resistant to corrosion and can handle a variety of fluids without degradation. This type of tubing is particularly useful in environments where chemical exposure is a concern. However, it may not be suitable for high-pressure applications like metal tubing.
Applications of Oil Well Tubing
Oil well tubing serves multiple applications across the oil and gas extraction process. Its primary function is to transport oil and gas to the surface, but it also plays a crucial role in maintaining the integrity of the well.
1. **Production Wells**: In production wells, oil well tubing is essential for extracting crude oil and transporting it to the surface facilities.
2. **Injection Wells**: In secondary recovery processes, tubing is used to inject water or gas into the reservoir to maintain pressure and enhance oil recovery.
3. **Monitoring Wells**: Tubing is also employed in monitoring wells to gauge reservoir conditions, including pressure and temperature.
Key Features and Specifications
When considering oil well tubing, specific features and specifications are crucial for ensuring optimal performance. Operators should pay close attention to the following:
- **Diameter and Length**: Tubing comes in various diameters and lengths, depending on the well's depth and the volume of hydrocarbons being extracted.
- **Wall Thickness**: The wall thickness of the tubing affects its strength and capacity to handle pressure.
- **Connection Type**: Different connection types, such as threaded or welded joints, offer varying levels of reliability and ease of installation.
- **Corrosion Resistance**: Depending on the environmental conditions, selecting tubing with adequate corrosion resistance is vital for longevity.
Maintenance Practices for Oil Well Tubing
Proper maintenance of oil well tubing is essential for ensuring its longevity and efficient operation. Here are some key practices:
1. **Regular Inspections**: Conducting regular inspections helps identify issues like corrosion, wear, or leaks before they become critical problems.
2. **Cleaning**: Routine cleaning of the tubing can prevent blockages and ensure smooth fluid flow.
3. **Pressure Testing**: Regular pressure testing can help detect any weaknesses or potential failures in the tubing system.
4. **Monitoring Fluid Composition**: Keeping track of the fluids being transported can help identify corrosive substances that may affect tubing integrity.
Best Practices for Selecting Oil Well Tubing
Choosing the right oil well tubing is crucial for efficient extraction and longevity. Consider the following best practices:
- **Assess Environmental Conditions**: Evaluate the specific environment of the well, including temperature, pressure, and fluid composition to select appropriate materials.
- **Consider Economic Factors**: Weigh the costs of different tubing options against their expected lifespan and maintenance needs.
- **Consult Industry Standards**: Refer to industry standards and regulations to ensure compliance and safety.
- **Engage with Suppliers**: Collaborate with tubing manufacturers and suppliers to gain insights into the best options for your specific operational needs.
Common Challenges and Solutions
The use of oil well tubing can present various challenges that operators must navigate.
1. **Corrosion**: One of the most common challenges is corrosion, particularly in harsh environments. Solutions include selecting corrosion-resistant materials and applying protective coatings.
2. **Blockages**: Tubing can become blocked due to scale buildup or debris. Regular maintenance and cleaning procedures can mitigate this issue.
3. **Wear and Tear**: Over time, tubing may experience wear and fatigue. Regular inspections and timely replacements of aging tubing can reduce the risk of failure.
Future Trends in Oil Well Tubing
The oil and gas industry is evolving, and so are the technologies and materials used in oil well tubing. Key future trends include:
- **Advanced Materials**: Research and development are ongoing in creating new materials that offer improved strength and corrosion resistance.
- **Smart Tubing Technologies**: The integration of sensors and monitoring systems within tubing is expected to enhance the ability to track and analyze well conditions in real time.
- **Sustainability Efforts**: The industry is moving towards more sustainable practices, including the development of biodegradable tubing materials.
Frequently Asked Questions (FAQs)
1. What is the primary function of oil well tubing?
The primary function of oil well tubing is to transport crude oil and gas from underground reservoirs to the surface while providing structural support to the wellbore.
2. How do I choose the right oil well tubing for my operations?
Consider environmental conditions, fluid composition, pressure requirements, and economic factors when selecting the appropriate oil well tubing.
3. What materials are commonly used for oil well tubing?
Common materials include carbon steel, stainless steel, and fiberglass, each offering unique benefits and drawbacks.
4. How often should oil well tubing be inspected?
Regular inspections should be conducted as part of routine maintenance, typically every few months or as dictated by operational conditions.
5. What are the signs of tubing failure?
Signs of tubing failure include pressure drops, unusual fluid flow rates, leaks, and visible corrosion or wear during inspections.
Conclusion
Understanding oil well tubing is vital for effective oil and gas extraction. By selecting the right type of tubing, adhering to maintenance best practices, and staying informed about new trends, operators can enhance the efficiency and longevity of their well systems. With proper knowledge and attention, oil well tubing can significantly contribute to the successful operation of extraction processes, ensuring a steady flow of hydrocarbons from the depths of the earth to the surface.
Hot Tags:
PREVIOUS: